Week 14 brought a mixed bag of news for the manufacturing sector highlighting both pockets of recovery and persistent challenges.
Let’s dive into the key developments starting with the encouraging signs from across the Atlantic.
The uptick in the US manufacturing index as reported by the Institute for Supply Management (ISM) offers a glimmer of hope after a concerning dip.
The rise to 55.3% in March from 54.2% in February suggests a stabilization potentially signaling a turning point after a two-year low.
However we need to be cautious about interpreting this as a robust recovery; it’s more of a hesitant step forward than a triumphant leap.
The underlying factors driving this improvement require further scrutiny before we can confidently pronounce a full-fledged resurgence.
We’ll delve deeper into the specifics of the ISM report later examining the components of the index to gain a clearer understanding of the nuances.
A Closer Look at the US Manufacturing Index
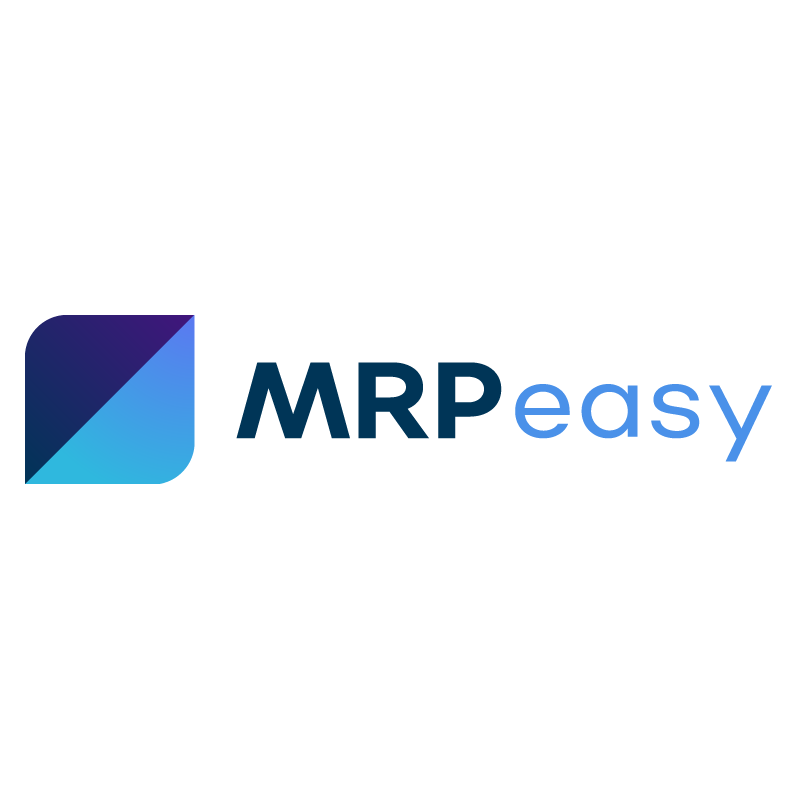
Dissecting the ISM Report: Beyond the Headline Number
The ISM’s manufacturing index is a composite indicator meaning it’s made up of several sub-indices reflecting different aspects of manufacturing activity.
Simply looking at the headline number – the overall index – can be misleading.
We need to examine the individual components such as new orders production employment supplier deliveries inventories customer inventories and prices to get a holistic picture.
For example a rise in new orders might suggest future growth potential even if current production levels haven’t yet fully rebounded.
Conversely a significant increase in inventories could signal weakening demand.
Analyzing these sub-indices reveals a far more nuanced and insightful picture than the headline figure alone.
The detailed breakdown allows us to identify potential bottlenecks or areas of strength within the manufacturing sector providing valuable context for strategic decision-making.
Analyzing the ISM data requires a deep understanding of economic indicators.
The index itself is a carefully weighted average of survey responses from purchasing managers carefully constructed to reflect the broader manufacturing climate.
Interpreting the data effectively hinges on understanding these weighting factors and the historical context of the index.
For example a seemingly small increase in one sub-index might be more significant than a larger rise in another depending on the weighting and past trends.
Sophisticated analysis often involves comparing the current data to historical averages seasonal adjustments and other economic indicators to provide more comprehensive insights into the state of the manufacturing economy.
Ignoring these crucial details can lead to seriously flawed interpretations of the market situation.
Navigating the Nuances of Manufacturing Data
Interpreting manufacturing data requires careful consideration of various factors influencing the reported figures.
For instance seasonal fluctuations can significantly impact monthly changes making year-over-year comparisons more reliable for identifying long-term trends.
Additionally the impact of global events – such as geopolitical instability supply chain disruptions or changes in commodity prices – needs to be factored into any comprehensive analysis.
This requires a deep understanding of global economics and the interconnectedness of various industrial sectors.
One cannot simply isolate the manufacturing sector and expect a fully accurate assessment without understanding its complex relationship with the wider economic landscape.
The data itself provides just a piece of the puzzle; we must use our expertise to understand the context in which the data is presented to draw meaningful conclusions.
Further complicating analysis is the fact that data from different sources may not align perfectly.
There’s an element of uncertainty built into any manufacturing data largely due to reporting lags and variations in methodology across various surveys and indices.
Reconciling these inconsistencies is a critical part of producing accurate and reliable insights.
A diligent analyst will actively seek to integrate data from multiple sources critically evaluating their respective methodologies and biases to arrive at a more comprehensive understanding.
Ultimately reaching informed conclusions requires deep knowledge of econometrics statistical analysis and an understanding of the limitations of the available data.
Ignoring these limitations leads to misinterpretations and inaccurate predictions.
The UK Manufacturing Landscape: A Sectoral Divide
The UK manufacturing sector presents a contrasting picture with growth heavily concentrated in a small number of industries.
MarketWatch highlighted the disproportionate reliance on food manufacturing motor vehicles transport equipment and machinery repair.
This concentration creates vulnerabilities.
Should significant challenges arise in these specific sectors – perhaps due to Brexit-related trade barriers – the impact on the overall UK manufacturing output could be disproportionately severe.
This sectoral imbalance underscores the need for a more diversified approach to economic growth within the UK manufacturing sector.
It highlights the risks associated with over-reliance on a few key industries and emphasizes the importance of fostering growth in other areas.
Brexit’s Lingering Shadow on UK Manufacturing
Brexit’s ongoing impact on UK manufacturing cannot be understated.
The introduction of new trade barriers has created uncertainty and increased costs for businesses.
This is particularly true for industries heavily reliant on imports and exports such as those mentioned earlier.
These new hurdles can stifle competitiveness limiting the UK’s ability to participate fully in the global market.
This situation is further exacerbated by the current global economic climate adding to the complexity of navigating the post-Brexit landscape.
The long-term effects of Brexit remain unclear with differing opinions amongst economists on the magnitude and nature of its overall impact.
The potential impact of Brexit on the four key sectors is particularly concerning given their significant contribution to overall manufacturing output.
Disruptions in supply chains increased customs procedures and the potential loss of access to the European single market could significantly hinder their growth.
The government’s response to this situation will play a significant role in mitigating the negative consequences.
Support mechanisms aimed at reducing the burden of new trade barriers and fostering innovation are crucial for mitigating the potential economic fallout.
It remains a critical policy challenge demanding careful consideration and strategic planning.
Diversification: A Path to Resilience
The UK’s over-reliance on a few key sectors is a cause for concern.
The lack of diversification exposes the UK manufacturing sector to considerable risk leaving it vulnerable to shocks within these specific sectors.
A more balanced approach is needed fostering growth in a broader range of industries to improve resilience.
This will entail targeted investments in research and development skills development and support for startups and small businesses.
This broader approach is essential to reduce the economic consequences of future disruptions whether those disruptions are caused by Brexit or unexpected external shocks.
The long-term sustainability and competitiveness of the UK manufacturing sector depend on actively pursuing this diversification strategy.
The High-Stakes World of ERP Implementations
The Financial Times report on the Worth & Co.
lawsuit over an ERP project highlights a major challenge faced by many businesses.
Large-scale ERP implementations are complex high-risk ventures often prone to cost and schedule overruns.
These overruns are not just financial burdens; they can disrupt operations damage morale and even lead to legal disputes.
The significant financial investments required underscore the need for meticulous planning realistic estimations and a deep understanding of the project’s complexities.
The Challenges of ERP Implementation
ERP systems are designed to integrate various aspects of a business from supply chain management to finance and human resources.
This week in manufacturing news was wild! 🤯 The US is showing signs of recovery, but the UK is struggling with Brexit blues. And don’t even get me started on ERP implementations – those things are a nightmare! 🤬
Want to learn more about how to navigate these challenges? Check out this awesome resource for insights and tips!
Successfully implementing an ERP system requires a multi-faceted approach that encompasses project management data migration system configuration employee training and ongoing support.
This complexity is often underestimated leading to delays and cost overruns.
Additionally the need to integrate data from various sources each with unique formats and structures adds significant complications.
Poor data quality insufficient training inadequate change management strategies and a lack of clear communication can all contribute to the failure of these large scale projects.
The inherent complexity of ERP systems makes them extremely susceptible to issues if not managed properly.
Often businesses under estimate the time and resources required to seamlessly migrate from their legacy system to a new ERP platform.
The migration process itself is a critical and delicate stage of implementation demanding careful planning testing and skilled expertise.
If this phase is not managed effectively businesses may find themselves facing data loss system errors or operational disruptions.
Furthermore providing adequate training to employees is crucial for the success of the project.
Training needs to be comprehensive covering all aspects of the new system and providing enough hands-on experience for employees to become proficient users.
Assessing the Return on Investment (ROI) of ERP Systems
The survey cited in the Financial Times report paints a sobering picture of ERP ROI.
Only 27% of businesses reported a positive ROI within two years.
This statistic highlights the significant risk associated with ERP projects.
Businesses must conduct thorough due diligence before embarking on an ERP implementation carefully assessing the costs and potential benefits and weighing the risks.
The key to achieving a positive ROI lies in careful project planning effective change management and a clear understanding of business needs.
An inadequate system selection process can lead to a mismatch between the business’s requirements and the capabilities of the selected ERP system.
The process of selecting an appropriate system involves a careful evaluation of various vendors and their offerings to ensure alignment between the software and the specific requirements of the organization.
Small Manufacturers and the Importance of MRP Software
The experience of Karl mentioned in the provided text highlights the specific challenges and opportunities facing small manufacturers.
This week in manufacturing news was wild! 🤯 The US is showing signs of recovery, but the UK is struggling with Brexit blues. And don’t even get me started on ERP implementations – those things are a nightmare! 🤬
Want to learn more about how to navigate these challenges? Check out this awesome resource for insights and tips!
His work at MRPeasy and contributions to industry publications underscore the importance of accessible user-friendly MRP (Material Requirements Planning) software.
Small manufacturers often lack the resources of larger companies making efficient inventory management and production planning critical for survival and growth.
MRP software can be a must for these businesses.
MRP Software: Empowering Small Manufacturers
MRP software helps small manufacturers optimize their production processes by providing real-time visibility into inventory levels production schedules and material requirements.
This enables them to make better decisions reducing waste minimizing delays and improving efficiency.
For small manufacturers such functionalities become especially vital due to their often more limited resources and capacity.
Efficient utilization of these resources is essential for their competitiveness.
The software provides a central hub for planning and tracking all aspects of their operations improving the collaboration and efficiency of their teams.
The implementation of MRP software presents an opportunity to enhance the overall profitability and efficiency of small manufacturers.
It enables them to address crucial challenges such as inventory optimization and production scheduling leading to substantial cost savings and reduced operational inefficiencies.
Adopting such advanced technologies can significantly improve their ability to compete effectively in the market improving both internal operations and the quality of their products and services.
This week in manufacturing news was wild! 🤯 The US is showing signs of recovery, but the UK is struggling with Brexit blues. And don’t even get me started on ERP implementations – those things are a nightmare! 🤬
Want to learn more about how to navigate these challenges? Check out this awesome resource for insights and tips!
Using technology effectively can set smaller companies apart from their competitors.
The Importance of Real-World Insights and User Feedback
Karl’s focus on incorporating real-life insights from manufacturers implementing MRP software is crucial.
Generic advice and theoretical concepts fall short in the practical realities of manufacturing.
Understanding the specific challenges and successes of small businesses provides invaluable knowledge and fosters improved software development and implementation strategies.
Feedback from users is instrumental in tailoring the software to meet the specific needs of diverse manufacturing operations.
Constant interaction and refinement are essential for ensuring that the software remains relevant and helpful to its users.
User feedback directly informs the design development and improvement of MRP software.
It allows developers to prioritize the features and functionalities that are most needed by manufacturers.
This iterative process ensures the software remains relevant usable and efficient for those who use it.
Active collaboration between software developers and small manufacturers is key for ensuring the success of MRP implementation.
By engaging with users and collecting their input software companies can create more effective and targeted solutions that genuinely enhance the efficiency of small manufacturers.
This collaborative approach is essential for bridging the gap between theoretical design and practical application.
In conclusion Week 14 in manufacturing news offered a mixed outlook.
While positive signs emerged in the US the UK highlighted sector-specific vulnerabilities.
The recurring issues with ERP implementations and the importance of MRP software for small manufacturers underscore the ongoing need for effective planning robust technology adoption and a data-driven approach to manufacturing decision-making.
Staying informed about these trends and nuances is essential for navigating the complexities of the ever-evolving manufacturing landscape.
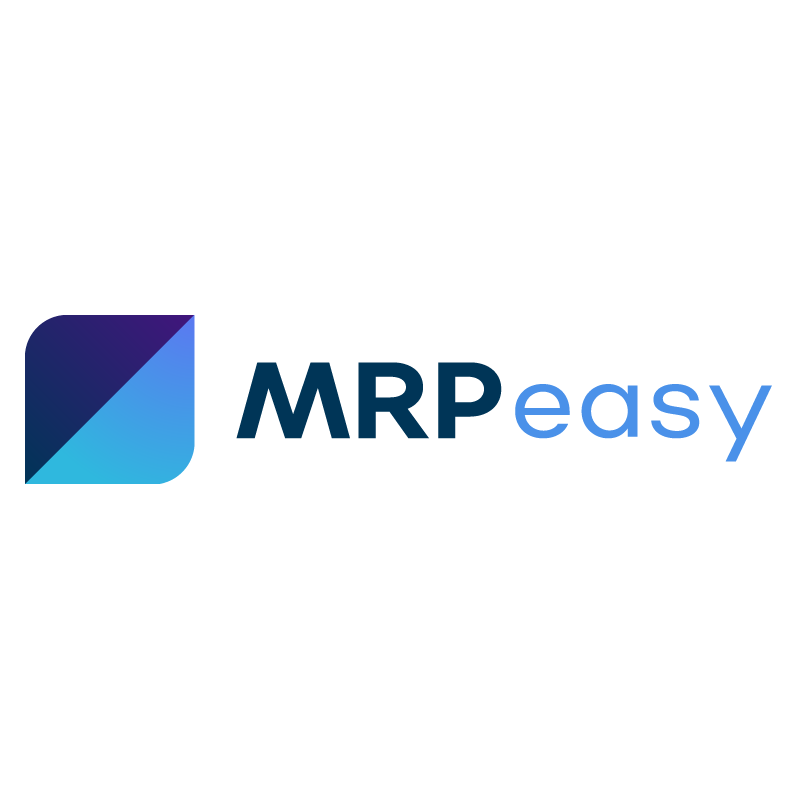