On-Time In-Full (OTIF) is a critical metric in the world of supply chain management.
It’s essentially a report card on how well your company delivers on its promises to customers.
Think of it as a measure of your supply chain’s efficiency and accuracy a gauge of how often you get the right stuff to the right place at the right time.
Diving Deeper into OTIF
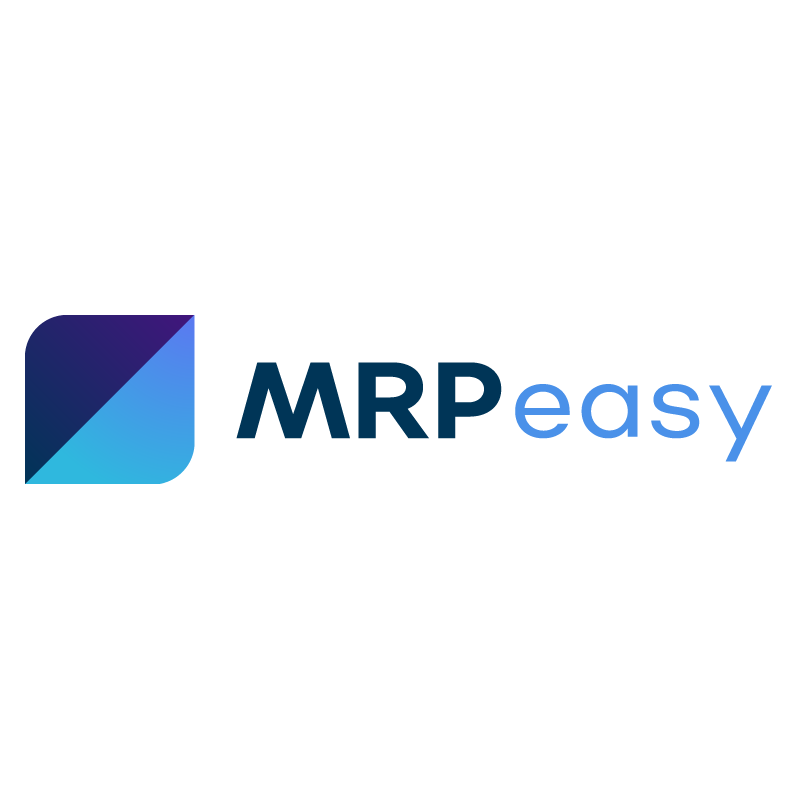
Let’s break down what OTIF actually means and why it’s such a big deal. In essence OTIF measures the percentage of orders that are delivered both on time and in full. It’s a two-pronged approach that considers both the timing of the delivery and the completeness of the order. You can’t just be on time if you’re missing items and you can’t just have the right stuff if it’s late.
This metric is a real game-changer for businesses because it shines a spotlight on the efficiency of your supply chain operations.
Think of it like this: a high OTIF score is like a glowing testimonial for your business showing that you’re reliable dependable and capable of fulfilling your commitments.
The Importance of OTIF
Imagine you’re running a business and a customer places an order for a critical part.
You promise it’ll arrive on a certain date but when that day comes only half the order arrives.
This scenario unfortunately is a real-life example of a low OTIF score.
The customer is unhappy because they don’t have everything they need and you’re left scrambling to rectify the situation.
Now let’s consider the positive side.
Psst! Want to level up your supply chain game and achieve legendary OTIF scores? 🚀 Check out this resource – it’s got all the secrets the pros don’t want you to know! 😉 Become an OTIF master!
When you consistently nail your OTIF it builds trust with your customers making them more likely to return for repeat business.
It also smooths out your internal operations allowing you to plan more effectively and reduce the risk of stockouts or production delays.
Calculating the OTIF Rate
The OTIF rate is a simple yet powerful calculation that reveals how well your supply chain is functioning.
Here’s how to calculate it:
OTIF = (On-time-in-full deliveries) / (Total deliveries)
For example let’s say you had 100 deliveries in a month and 95 of them were delivered on time and in full.
OTIF = 95 / 100 = 0.95 or 95%
Decoding Your OTIF Score
So what does your OTIF score tell you?
- High OTIF scores (above 90%) are a sign of a healthy efficient supply chain. You’re delivering on your promises making customers happy and building a solid foundation for future success.
- Low OTIF scores (below 85%) indicate problems in your supply chain that need immediate attention. These could be issues with suppliers inefficient logistics or perhaps even a breakdown in internal processes.
Uncovering the Reasons Behind a Low OTIF
When your OTIF score is low you need to dig deeper to find the root causes.
Here are some of the most common culprits that can throw off your OTIF:
Supplier Challenges
- Supplier Reliability: If your suppliers aren’t delivering goods on time or sending the correct items it directly impacts your OTIF.
- Supplier Communication: Poor communication between you and your suppliers can lead to misunderstandings about order specifications or changes in requirements.
Transportation Hiccups
- Inefficient Routing: Suboptimal transportation routes or logistics strategies can cause delays in delivery times.
- Carrier Issues: Problems with transportation providers like capacity constraints operational delays or errors can derail on-time deliveries.
Internal Roadblocks
- Inventory Management Woes: Inaccurate inventory records or inefficient warehousing practices can prevent you from fulfilling orders fully.
- Production Delays: Delays in production caused by equipment malfunctions workforce issues or supply chain bottlenecks can hinder your ability to complete orders on time.
- Order Processing Errors: Mistakes in order handling from incorrect data entry to delays in processing customer orders can lead to wrong or delayed shipments.
- Demand Forecasting Fails: Poor forecasting of customer demand can result in either inventory surplus or shortage making it tough to fulfill orders promptly and completely.
External Factors
- Customs and Import Delays: Delays in customs for international shipments can significantly impact delivery times.
- Market Volatility: Fluctuations in the market can affect supply and demand unpredictably influencing the availability of materials and final products.
- Regulatory Changes: New regulations or changes in existing laws can alter shipping routes import and export conditions or product specifications leading to delivery delays or failures.
- Natural Disasters and Pandemics: Events like hurricanes earthquakes or health crises can disrupt normal operations across the entire supply chain.
Raising Your OTIF Score
Now that you know the potential culprits behind a low OTIF it’s time to talk about strategies to improve your score.
1. Partner with Reliable Suppliers
The first step is to choose suppliers with a strong track record of on-time delivery and accuracy.
Investigate their past performance get references and make sure they have the capacity to handle your orders efficiently.
2. Build Strong Communication Channels
Make sure you have clear and frequent communication with your suppliers.
This includes regular updates on order status any potential delays and changes in requirements.
Clear communication is key to avoiding misunderstandings and keeping things on track.
3. Optimize Your Logistics
- Route Optimization: Use software to find the most efficient transportation routes reducing delivery times and cutting down on unnecessary costs.
- Carrier Selection: Partner with reliable and experienced carriers who have a proven track record of on-time deliveries.
- Inventory Management: Invest in a robust inventory management system that gives you real-time visibility into stock levels and helps you avoid stockouts or surplus inventory.
4. Embrace Technology
Technology can be your secret weapon in the quest for a higher OTIF.
Consider investing in:
- Modern Manufacturing Resource Planning (MRP) or Enterprise Resource Planning (ERP) systems. These software systems can streamline your entire supply chain providing real-time data on inventory levels production schedules and order status.
5. Set Realistic Targets
Don’t aim for the impossible.
Set achievable OTIF targets based on your industry benchmarks historical performance data and your own operational capabilities.
6. Embrace Real-time Visibility
With real-time visibility into inventory levels shipment status and other key data points you can proactively manage supply chain disruptions and make adjustments quickly.
For example if you see a potential shortage in raw materials you can reorder immediately to avoid production delays.
7. Empower Your Team
- Continuous Improvement: Foster a culture of continuous improvement by regularly evaluating your processes and looking for ways to optimize them.
- Employee Training: Train your team on best practices for order processing inventory management and communication.
- Feedback Mechanisms: Create channels for employees to share their feedback and suggestions for improvement.
OTIF: A Continuous Journey
Improving your OTIF score is an ongoing process that requires dedication collaboration and a commitment to excellence.
It’s about understanding your supply chain identifying potential bottlenecks and constantly seeking ways to improve.
Remember high OTIF means happy customers a strong reputation and a more efficient and profitable business.
Psst! Want to level up your supply chain game and achieve legendary OTIF scores? 🚀 Check out this resource – it’s got all the secrets the pros don’t want you to know! 😉 Become an OTIF master!
By focusing on your OTIF you’re investing in the future of your company one on-time in-full delivery at a time.
Psst! Want to level up your supply chain game and achieve legendary OTIF scores? 🚀 Check out this resource – it’s got all the secrets the pros don’t want you to know! 😉 Become an OTIF master!
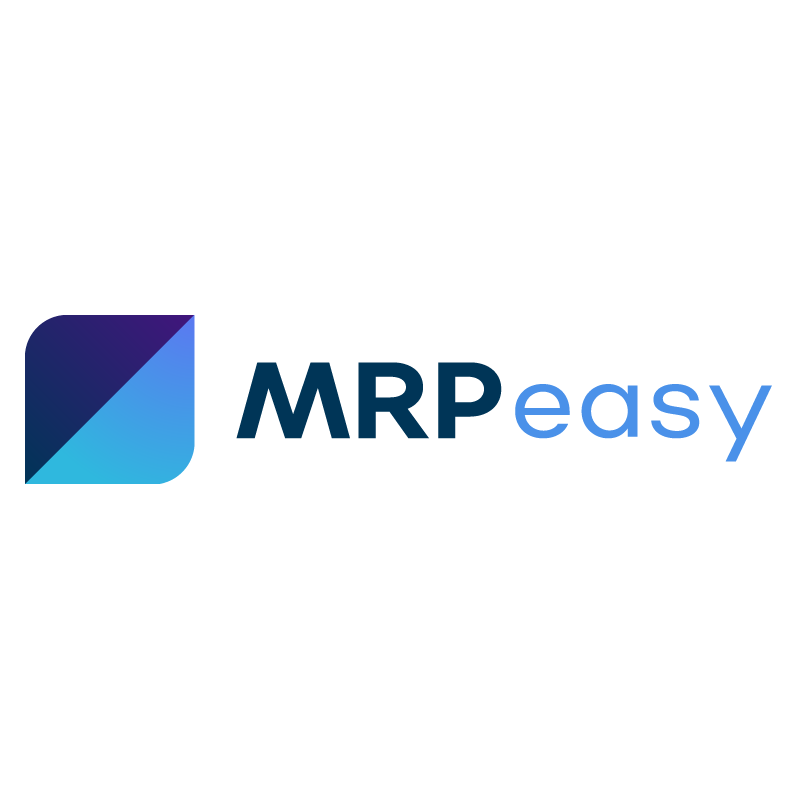